高精度の傾き/角度検出において最高の性能を得る方法、必要なのは応力と歪みの管理
はじめに
加速度センサーを使用すれば、様々な用途において静的/動的な加速度を検出することができます。例えば、重力に対する機器の傾きを計測するといった具合です。実際、携帯電話を傾けた際に表示方向を変更する機能も、加速度センサーを使用して実現されています。また、壊れ始めた橋の微かな動きを検出するという用途にも利用できます。更に、輸出規制の対象となる戦術グレードの機器でも加速度センサーは活用されています1。そうした機器は、宇宙船や防衛用車両などの操縦に利用されます。上記の例からも明らかなように、加速度センサーを搭載するシステムは、理想的な環境で使われるとは限りません。用途によっては、温度をはじめとする制御不能で過酷な環境要因からの多大なストレスにさらされることになるでしょう。ほとんどの加速度センサーは、そうした条件の下で、実験室で得られるのと同等の性能を発揮することはできません。加速度センサーが過大なストレスを受けた結果、その影響によってシステムが故障してしまう可能性もあります。
高い精度が求められる傾き検出システムでは、1°未満の測定精度を達成できるようにキャリブレーションが実施されます。アナログ・デバイセズは、「ADXL354」や「ADXL355」など、市場を牽引する超低ノイズで安定性の高い加速度センサーを提供しています。そうした製品を使用すれば、観測が可能な誤差要因に対して適切にキャリブレーションを実施することで、0.005°という優れた傾き測定の精度を達成することができます2。但し、このレベルの精度を達成できるのは、応力が適切に軽減されている場合だけです。例えば、加速度センサーに圧縮応力や引張応力がかかると、20mgものオフセット誤差が生じることがあります。そうすると、傾きの測定誤差が1°以上に達してしまうかもしれません。
本稿では、加速度センサーを使用した角度/傾き検出システムにおいて高い測定精度を実現する方法について説明します。まずは、応力と歪みの影響について正しく理解できるようにするために、加速度センサー自体がどのように構成されているのか紹介することから始めます。続いて、ADXL355を採用した計測システムに関する数々の実験結果をご覧いただきます。それにより、機械的/物理的な面で包括的な設計手法を採用しなかった場合には、どのようなことが待ち受けているのか、把握することができるでしょう。更に、非常に要件の厳しいアプリケーションにおいて性能を最大限に高めるために採用すべき設計上のノウハウを紹介します。
ADXL35xの内部設計
ADXL354/ADXL355は、MEMS(Micro Electro Mechanical Systems)ベースの加速度センサーです。この種のセンサーは、価格と性能の面で、民生分野から航空宇宙/防衛分野までの広範な用途に対応できます。アナログ・デバイセズの加速度センサー製品群の中で、ノイズ性能を含めて最も高い能力を実現しているのがADXL354/ADXL355です。両製品は、高精度の傾き検出、地震探査、ロボットやプラットフォームの安定化といった多くの新しいアプリケーションに適用することができます。ADXL354は、アナログ出力方式の加速度センサーです。この製品は、あらゆるアナログ・データ・アクイジション・システムに接続することができます。一方のADXL355は、市場をリードする特徴を備えており、高精度の傾き/角度検出アプリケーション領域において、他に類を見ない存在になっています。例えば、ノイズ、オフセット、再現性、温度に依存するオフセットといった性能の面で非常に優れています。加えて、振動整流や交差軸感度といった2次的効果の面でも優位性を持ちます。そこで、本稿では、高精度の加速度センサーの例としてADXL355を取り上げることにします。ここで説明する内容は、ADXL355に固有の話ではなく、3軸MEMS加速度センサーの大半に当てはまります。
ADXL355を最適な状態で動作させるためには、システム設計においてどのようなことを考慮すべきなのでしょうか。これについて理解するには、加速度センサーの内部構造を把握しておく必要があります。そうすると、例えば面外応力などの環境パラメータに対し、3つの軸が異なる反応を示す理由を理解することができます。多くの場合、面外応力による測定誤差は、センサーのZ軸における温度勾配が原因で生じます。
ADXL35xファミリの製品は、他の多くのMEMS加速度センサーと同様にバネ質量系として構成されています。外部加速度(重力のような静的加速度または速度の変化のような動的加速度)が生じると、それに応答して質量が動きます。その際の物理的な変位が変換機構によって検出されます。MEMSベースのセンサーの一般的な変換機構としては、静電容量検出方式、ピエゾ抵抗方式、圧電方式、磁気検出方式が挙げられます。これらのうち、ADXL355は静電容量検出方式の変換機構を採用しています。質量の動きは、読み出し回路により、静電容量の変化を電圧出力または電流出力に変換することで検出します。ADXL355の場合、シリコン・ダイ上の3種のセンサーは、いずれも静電容量検出方式の変換機構を採用しています。但し、X軸/Y軸センサーとZ軸センサーは、根本的に異なるアーキテクチャを採用しています。図1に示すように、X軸/Y軸センサーでは同一面内の差動櫛歯電極を使用します。それに対し、Z軸センサーは面外の平行平板静電容量センサーを使用します。

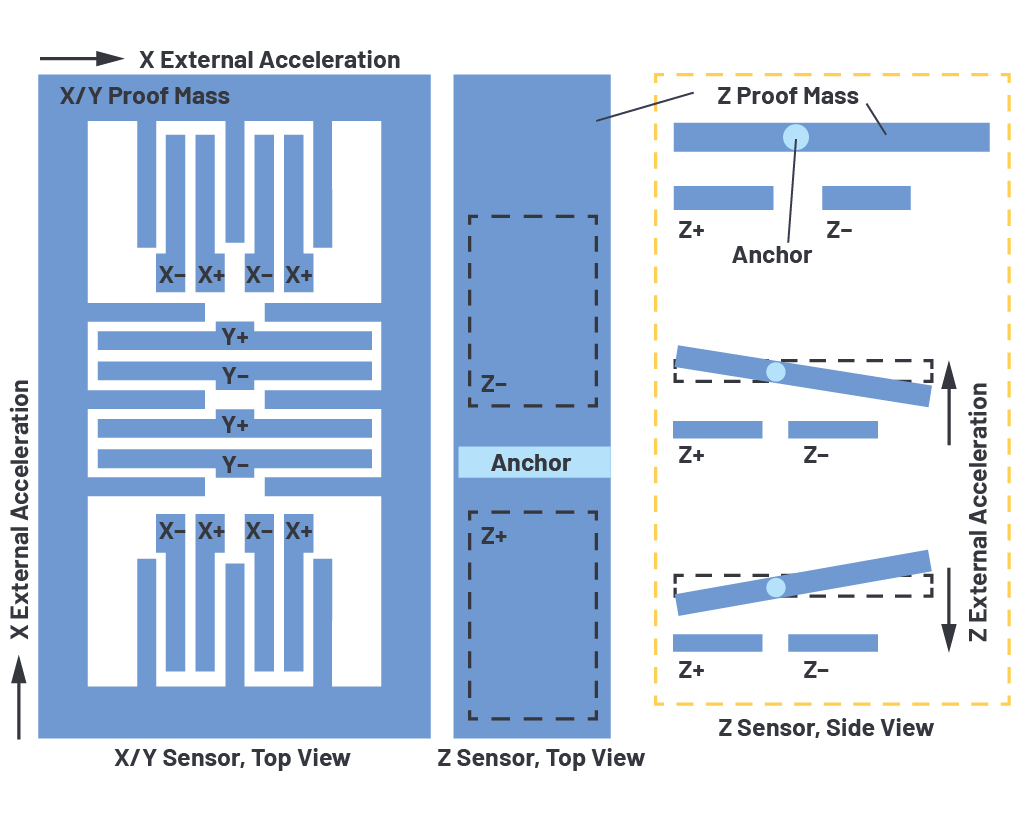
図1. ADXL355のセンサー・アーキテクチャ。X軸/Y軸センサーでは、プルーフ・マスが動くと、固定櫛歯電極とプルーフ・マスに取り付けられた櫛歯電極の間の静電容量が変化します。Z軸センサーの質量がアンバランスになっているため、Z軸方向の加速度の面外検出が可能になります。
センサーに圧縮応力または引張応力が働くと、ダイに反りが生じます。ダイの基板において、プルーフ・マス(錘質量)はバネで吊るされています。そのため、プルーフ・マスは基板と連動して反ることはありません。結果として、プルーフ・マスと基板のギャップ(間隙)が変化することになります。X軸/Y軸センサーにおいて、櫛歯電極の静電容量の変化に対しては、面内変位が最も大きな影響を及ぼす要因になります。つまり、プルーフ・マスと基板のギャップは、静電容量の感度については重要な影響因子にはなりません。これは、フリンジ電界の補償効果に依存します。一方、Z軸センサーでは、プルーフ・マスと基板のギャップが検出の対象になります。このギャップが応力によって変化するということは、Z軸センサーの測定結果には応力の影響が直接及ぶということを意味します。また、Z軸センサーがダイの中央に位置していることも、測定に悪影響を及ぼす要因になります。ダイに何らかの応力がかかると、その位置での反りが最も大きくなるからです。
ほとんどのアプリケーションでは、物理的な応力に加え、Z軸方向に伝わる熱の非対称性によって、Z軸センサーの全体にわたって温度勾配が生じます。一般的なアプリケーションでは、センサーはプリント回路基板にハンダ付けされ、システム全体がパッケージに収められます。X方向とY方向については、パッケージ周囲のハンダ接合部を介した熱伝導と基板への熱伝導が支配的かつ対称的に発生します。それに対し、Z方向では、ハンダを介した底面における伝導と、ダイ上面での対流によって熱が伝わります。ダイ上面での対流というのは、空気を介してパッケージの外へ熱が移動するということです。このように、X軸/Y軸とZ軸とでは、熱伝導の仕組みが異なります。その結果、Z軸については残留温度勾配差が生じることになります。つまり、Z軸センサーでは、物理的な圧縮応力/引張応力だけでなく、温度勾配も原因となって測定誤差が発生します。言い換えると、Z軸センサーでは、加速度とは関係なくオフセットが観測されるということです。
環境ストレスを考慮してデータを検証する
ここからは、ADXL355に関する各種の実験結果を示すことにします。それらの実験には、フォーム・ファクタの小さい評価用ボード「EVAL-ADXL35X」を使用することにしました。ADXL355の評価用ボードは、お客様のシステムに直接取り付けられるように設計されています。そのため、既存の組み込みシステムを用いて簡単にプロトタイピングを実施することができます。ここでは、データのロギングと解析を行えるようにするために、EVAL-ADXL35Xをマイクロコントローラ・ボード「SDP-K1」に接続し、Mbed®環境を使用してプログラミングを実施しました。Mbedは、ARM®ベースのマイクロコントローラを搭載したボード向けに提供されているオープンソースの開発環境(無償)です。この環境にはオンライン・コンパイラが用意されていることから、必要な作業をすぐに開始することができます。SDP-K1は、PCに接続すると外部ドライブとして扱われます。コンパイラによって生成されたバイナリ・ファイルをSDP-K1のアイコンにドラッグ&ドロップするだけで、同ボードのプログラムが完了します3、4。
ここでは、Mbedベースのシステムにより、UART(Universal Asynchronous Receiver/Transmitter)を介してデータのロギングを実行できるようにしました。このようにすると、ADXL355を使って簡単に実験を行ったり、データのロギングや詳細な解析のために単純な端末に出力をストリーミングしたりすることが可能になります。つまり、基本的な実験環境が整うということです。ここで注意が必要なのは、加速度センサーの出力データ・レートに関わらず、Mbedのコードではレジスタを対象としたロギングを2Hz周期でしか実施できないということです。Mbedを使ってより速いレートでロギングすることも可能ですが、ここではその方法についての説明は割愛します。
実験を行う際には、最初に適切なデータを取得することが重要です。そうすれば、基準になる性能を定めることができます。また、その後のほとんどのデータ解析において、どのようなノイズ・レベルを想定すべきか確認するのが容易になります。この実験環境では、吸盤マウントを備える多関節バイス・アーム(PanaVise製)5を使用することにしました。これであれば、ガラス製の作業面に張り付けることができます。その結果、作業台において適度に安定した作業面を使用することが可能になります。このような構成により、ADXL355のボード(側面から保持)を実験室の作業台と同程度に安定させることができます。このバイス・アームを使用する方法では、傾斜の動きに関して何らかのリスクが生じる可能性があります。それでも、これは重力に対する方向を変更可能な簡易で費用対効果の高い方法だと言えます。ADXL355のボードは、図2に示すようにバイス・アームに取り付けました。その上で、最初の解析を行うために60秒間分のデータを取得しました。

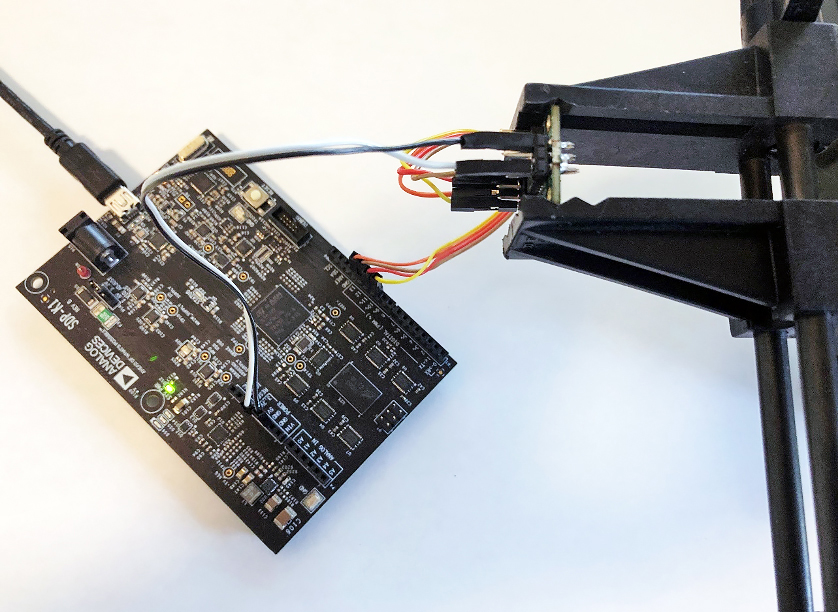
図2. 実験環境の外観。EVAL-ADXL35X、SDP-K1、多関節バイス・アームを使用して構成しました。

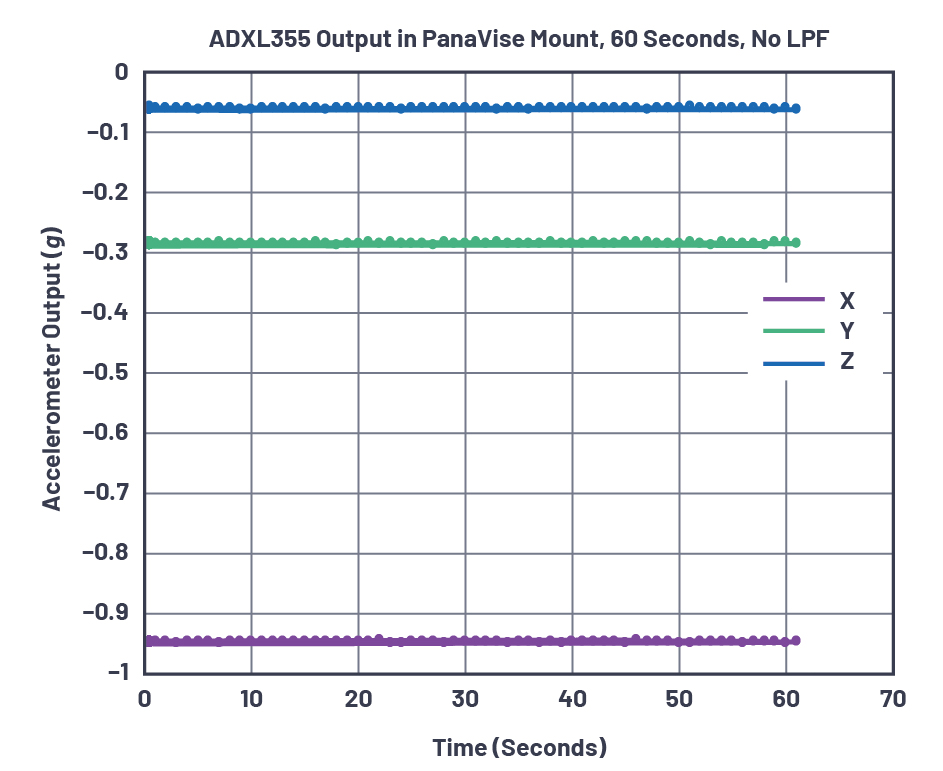
図3. ADXL355の出力データ(その1)。LPFは使用せず(レジスタ0x28に0x00を設定)、60秒間にわたって取得しました。
120個のデータ・ポイントを取得して標準偏差を求めたところ、ノイズの範囲は800μg~1.1mgとなりました。ADXL355のデータシートを見ると、標準的なノイズ密度は25μg/√Hzだということがわかります。ローパス・フィルタ(LPF)をデフォルトの設定で使用する場合、ADXL355の帯域幅は約1000Hzになります。LPFがブリック・ウォール・フィルタであると仮定すると、ノイズは25μg/√Hz×√1000(Hz) = 791μg rmsになると予測できます。最初に取得したデータセットは、最初のスニッフ・テストに合格したと言えます。実際のLPFは、無限大のロールオフ性能を備えるブリック・ウォール・フィルタではありません。そのため、ノイズ・スペクトル密度からrmsノイズへの変換を行う際には、デジタルLPFに対応する係数を適用する必要があります。20dB/decadeのロールオフ性能を備えるシンプルなRC単極フィルタでは、1.6倍という係数がよく使用されます。しかし、ADXL355が備えるデジタルLPFは、単極RCフィルタでもありません。とはいえ、1~1.6の係数を想定すれば、ノイズの予測結果として適切な近似値が得られるはずです。
高い精度が求められるセンシング・アプリケーションでは、多くの場合、1000Hzという帯域幅は測定する信号に対して広すぎます。帯域幅とノイズの間のトレードオフを最適化するために、ADXL355ではデジタルLPFを利用できるようになっています。そこで、続いてはLPFの帯域幅を4Hzに設定することにしました。そうすると、ノイズは1/16(√1000/√4≒16)に低減されるはずです。このような設定の変更は、Mbed環境であれば簡単に実行できます。必要なのは、図4に示す単純なコードを追加することだけです6。その結果、得られたデータを図5に示しました。上記のLPFを適用したことで、ノイズは予想どおり低減しています。表1に、LPFを使用しない場合と使用する場合の結果をまとめました。

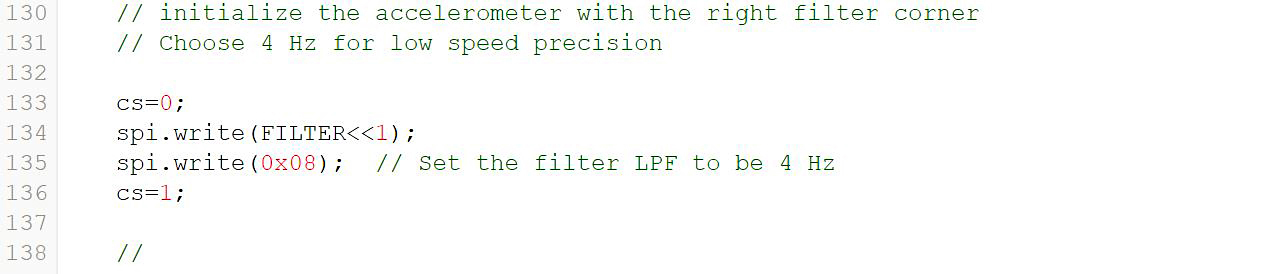
図4. Mbedのコード。レジスタの設定に使用します。

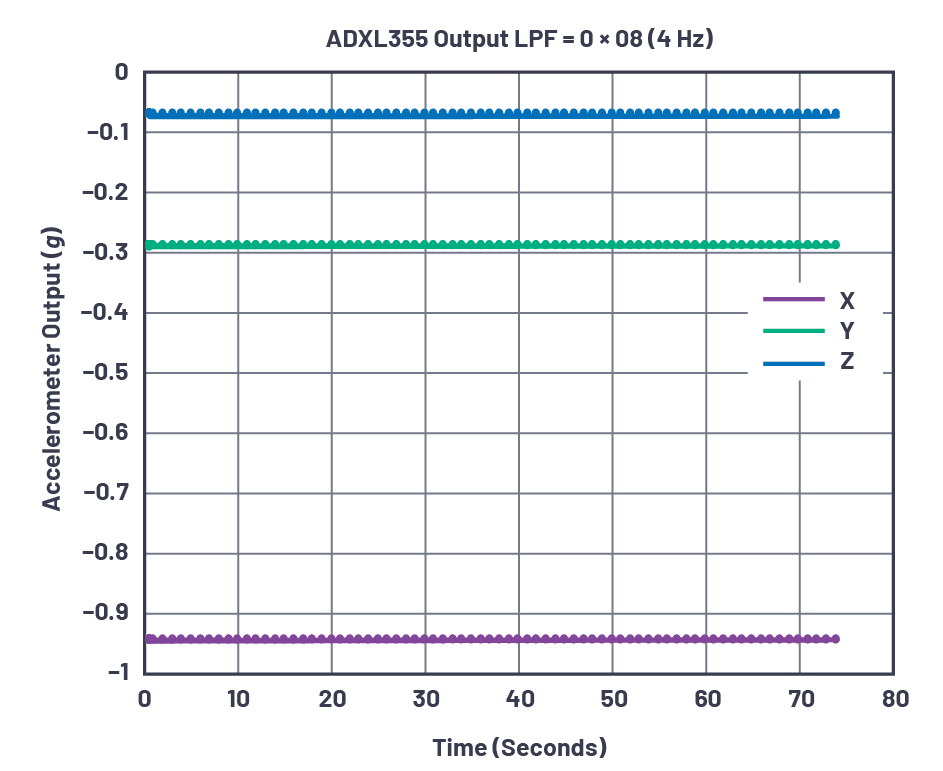
図5. ADXL355の出力データ(その2)。レジスタ0x28に0x08を設定することで、LPFの帯域幅を4Hzに変更しました。60秒間にわたってデータを取得しています。
ノイズ | X | Y | Z | |||
予測値〔μg〕 | 実測値〔μg〕 | 予測値〔μg〕 | 実測値〔μg〕 | 予測値〔μg〕 | 実測値〔μg〕 | |
フィルタなし | 791 | 923 | 791 | 1139 | 791 | 805 |
4Hzのフィルタ | 50 | 58 | 50 | 185 | 50 | 63 |
表1のとおり、この設定ではY軸のノイズの実測値が予測値(理論値)よりも大きくなっています。何が原因なのか調査した結果、実験環境で使用している他の機器が原因として浮上しました。ノートPCが備えるファンなどの振動がノイズとしてY軸に現れている可能性があったということです。これについて確認するために、バイス・アームを回転させてY軸があった位置にX軸が来るようにしました。その結果、X軸のノイズが高くなりました。このことから、X軸とY軸のノイズの差は、周辺機器類の影響によって生じているということがわかりました。つまり、ADXL355のX軸センサーとY軸センサーにおいて、ノイズ・レベルに本質的な差があるわけではないということです。このような確認作業は、プログラムを作成する際、試しに「Hello World」という文字列を出力するコードを記述してみるのと同じことです。低ノイズの加速度センサーを評価する際には、このような実験を随時行ってみるとよいでしょう。そうすれば、自信を持って次の作業に進むことができます。
続いて、熱衝撃はADXL355の測定結果に対してどの程度の影響を及ぼすのか評価しました。まずは感覚をつかむために、Weller製のホット・エア・ガン7を冷風モードで動作させ、加速度センサーに熱応力を加えました。このエア・ガンの場合、冷風モードでも室温より数℃高いエアが吹き出します。温度については、ADXL355が内蔵する温度センサーを使用してロギングすることにしました。この実験では、バイス・アームを使ってADXL355が垂直になるよう配置しました。エア・ガンによってパッケージ上面にエアを吹きつけられるようにするためです。この実験の結果としては、ダイを加熱することにより、温度係数を伴うオフセットが生じるとの予想が成り立つはずです。但し、熱応力の差は瞬間的に現れるということには注意が必要です。そのため、個々の軸が熱応力の差に敏感であるなら、時間軸でモニターすると、加速度センサーの出力プロットに隆起が現れると予想されます。なお、データの変化が小さい場合には、各データと平均値の差をとるとよいでしょう。そうすれば、3軸の比較を同時かつ容易に行えます。そのようにして取得した結果を図6に示しました。

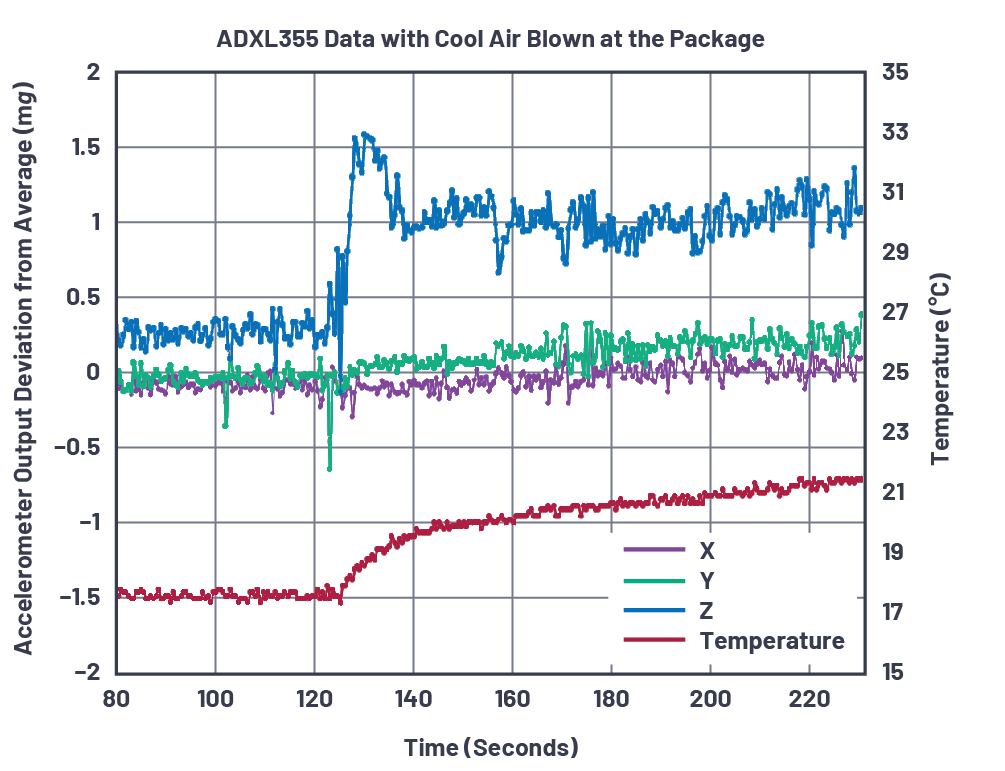
図6. 冷風モードによってパッケージにわずかな熱を加えた場合のADXL355の出力
図6には温度の変化も示してあります。この実験では、エア・ガンによって、気密封止されているセラミック・パッケージにわずかに温度が高いエアを吹きつけました。それにより、Z軸には約1500μgの変動が生じています。Y軸の変動量はそれよりもはるかに小さく(100μg程度)、X軸ではほぼ変動は生じていません。加速度センサーを使用する機器の多くは、プリント基板の上面に何らかの筐体を設けて熱応力の差が分散するように設計されます。その際には、このような種類の高速かつ過渡的な応力についても考慮しなければなりません。ここで示した実験結果と同様に、この種の応力による影響は、オフセット誤差として現れる可能性があります。
図7に示したのは、冷風モードで動作していたエア・ガンを停止したときの結果です。この場合、図6とは逆に温度がやや下降することになります。

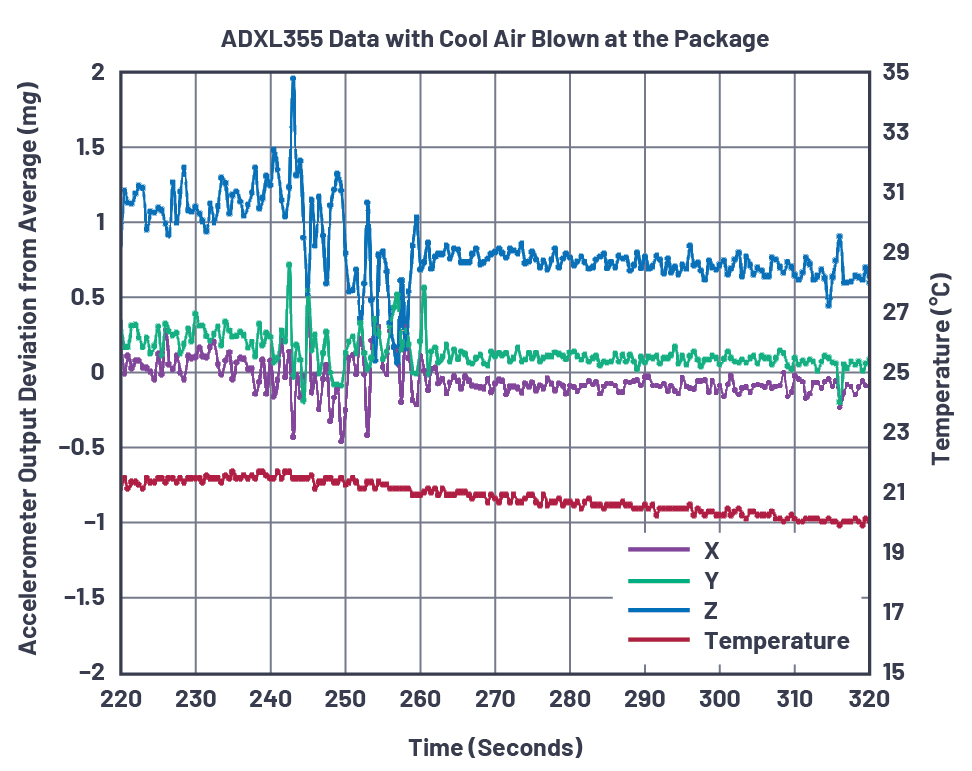
図7. エア・ガンを停止したときのADXL355の出力。グラフ上の240秒の時点でエア・ガンを停止させました。そこから温度の降下が始まっています。
次に、エア・ガンを加熱モードで動作させてより大きな熱衝撃を加えました。当然のことながら、影響はより顕著になります。過熱モードでは、エア・ガンから約400°Cのエアが送出されます。したがって、ボードの過熱や熱衝撃による損傷を避けるために、少し離れた位置からエアを吹きつける必要があります。具体的には、約15cm離れた場所から熱風を吹きつけました。その結果、ほぼ瞬時に約40°Cの温度変動が発生しました(図8)。

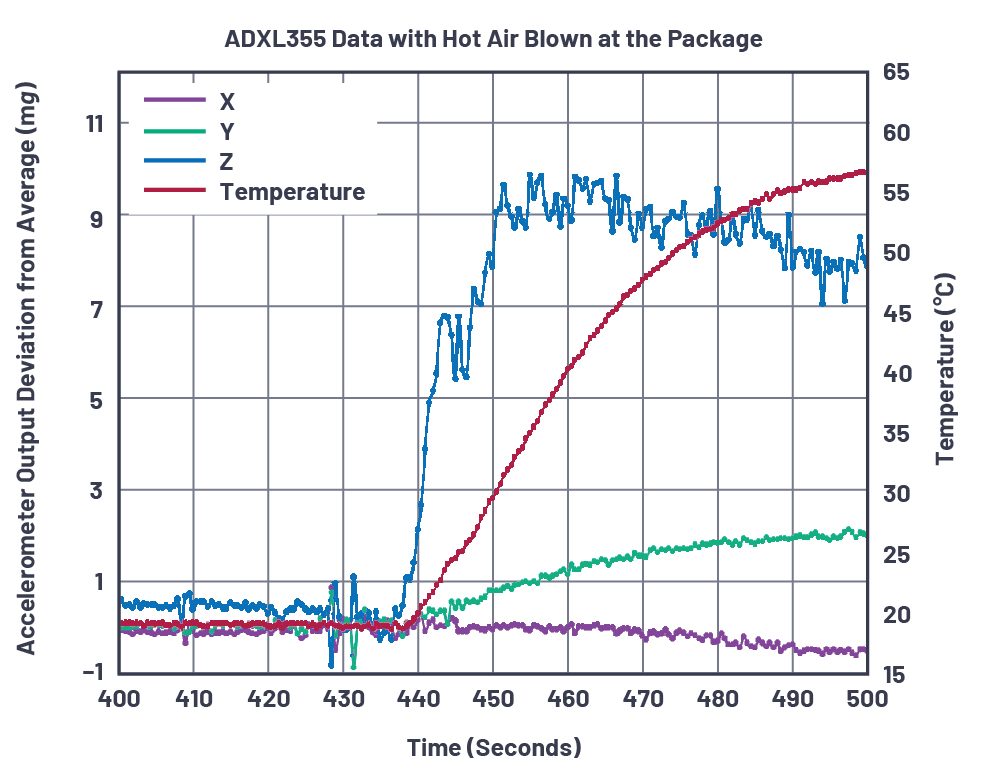
図8. パッケージに熱風を吹きつけた場合のADXL355の出力
この実験結果を見ると、X軸、Y軸と比較して、Z軸には非常に大きな影響が現れています。ただ、データシートに記載されたオフセットの温度係数を用いて計算すると、温度が40°C変動した場合でも、測定値の変動は100μg/°C×40°C = 4mg程度に収まるはずです。また、X軸とY軸の変動は少し時間が経ってから現れていますが、Z軸ではほぼ瞬時に10mgの変動が生じています。これらの事実から、Z軸のオフセットは温度そのものが原因で生じているわけではないと考えられます。実は、これはセンサーに対する熱応力の差と歪みによって生じた結果です。先述したように、ADXL355では、X軸、Y軸と比較すると、応力の差に対してZ軸がより敏感に反応します。そのため、Z軸において最も顕著な変動が観測されたのです。
ADXL355のデータシートを見ると、オフセットの標準的な温度係数(offset tempco)は±100μg/°Cとなっています。この温度係数は、加速度センサーをオーブンの中に入れた状態で計測します。その際には、センサーの動作温度範囲の全体わたってゆっくりと温度を変化させていきます。このような条件下でオフセットの値を取得し、温度変化に対するプロットの傾きを計測します。今回の実験とは、この点が大きく異なることを理解しておく必要があります。オーブンを使った手法で計測を行うと、図9に示すような結果が得られます。

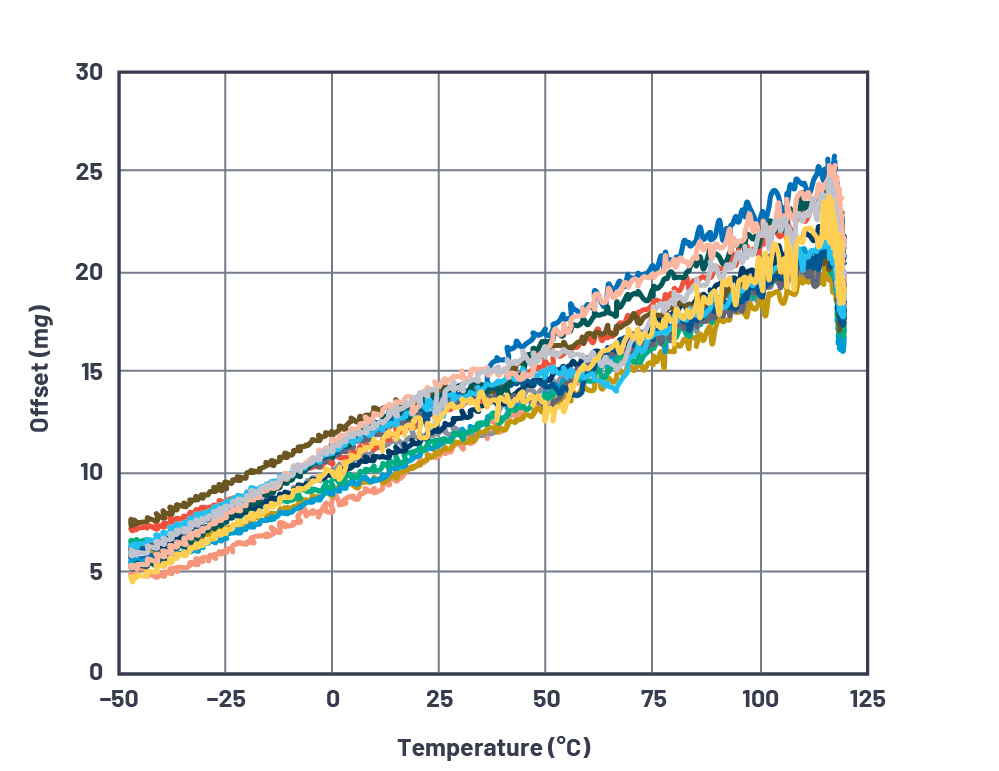
図9. オーブンを使用してADXL355の温度特性を評価した結果
図9の結果を見ると、影響を及ぼす要因が2つ存在することがわかります。1つは、データシートに記載されているオフセットの温度係数です。逆に言えば、その温度係数は、このような特性評価を経て算出されています。その際には、オーブンによって一定の温度に保持するわけではありません。そうではなく、5°C /分のペースで温度を上昇させていきます。そのような手法により、多数のデバイスを-45°C~120°Cの範囲で動作させ、得られた結果の平均をとります。ここで、図9のプロットを基にオフセットの温度係数を算出してみましょう。図9を見ると、165°Cの温度範囲に対してオフセットが約18mg変動しているので、温度係数は約109μg/°Cになります。データシートに記載された標準値は100μg/°Cなので、それよりもやや大きくなっています。それでも、データシートで規定されている最小値から最大値の範囲内には収まっています。ただ、図9の右端の部分については詳しく検討する必要があります。実は、この部分では、約15分にわたりデバイスを120°Cで保持するということが行われています。そのようにしてデバイスを高温の状態で保持すると、オフセットの量はやや低下します。平均値は165°Cの温度範囲に対して10mg近くになり、温度係数は60μg/°C程度になります。このグラフに影響を及ぼしている2つ目の要因は熱応力の差です。センサー内部のプルーフ・マスがデバイス全体の温度で安定し、応力が低減するという状況が生じます。その影響は、図6から図8に示した結果に現れています。ここで理解すべきことは、その影響が非常に短い時間で生じているということです。データシートに記載されているオフセットの温度係数は、長い時間をかけて計測された値であり、それとは条件が異なります。多くのシステムでは、温度の変化があるとしても、その速度は5°C /分よりはるかに遅くなります。そのため、多くのシステムにとって、上記の特性は有益である可能性があります。
ADXL355の安定性に影響を及ぼすその他の要因
ここまでで、加速度センサーに対する熱応力の影響について理解を深めることができたはずです。次に検討すべきことは長期安定性(再現性)についてです。つまり、同一の条件下であれば、長期間にわたって継続的に正確な測定結果が得られるのかということを確認する必要があります。その評価方法としては、次のようなものが考えられます。まず、ある温度条件の下、重力に対して同一の方向で重力場の測定を行います。そして、長い時間が経過した後、同一の温度条件下で再び重力場の測定を実施します。それら2つの結果がどの程度一致しているのか評価することで、再現性を確認することができます。定期的なキャリブレーションを実施することができないアプリケーションでは、センサーの長期安定性を評価する際、オフセットと感度の再現性が非常に重要な指標になります。ところが、センサー・メーカーの多くは、自社製品の長期安定性の評価を実施していません。また、データシートにもそれに関する記載はありません。それに対し、ADXL355のデータシートには、10年の寿命を想定した再現性の予測値が記載されています。また、高温動作寿命試験(HTOL:High Temperature Operating Life Test)の結果として、測定値の変動量が示されています。このHTOLは、150°Cの温度、3.6Vの電源電圧、1000時間の動作という条件で実施されます。更に、-55°C~125°C、1000サイクルの温度サイクル試験や、速度ランダム・ウォーク、広帯域ノイズ、温度ヒステリシスの各試験結果も掲載されています。ADXL35xファミリの製品は、データシートに記載されているとおり、優れた再現性を備えています。ADXL355の場合、X軸/Y軸センサーとZ軸センサーの再現性は、それぞれ±2mg、±3mgです。
機械的、環境的な条件に加え、慣性の条件も安定している場合、再現性は時間に対する平方根則に従います。例えば、X軸のオフセットについて、2.5年の使用期間(おそらく最終的な機器にとっては短いミッション・プロファイル)が経過した後の再現性は、±2mg×√(2.5年/10年) = ±1mgといった具合に算出することができます。図10に示したのは、HTOLを実施してオフセット・ドリフトを計測した結果です。32個のデバイスを使用し、0gにおけるオフセット・ドリフトを23日間にわたって計測しました。このグラフを見ると、平方根則がはっきりと確認できます。また、MEMSセンサーの製造ばらつきによって、各デバイスの性能に差が出ることもわかります。このような製造ばらつきのことも、正しく認識しておかなければなりません。

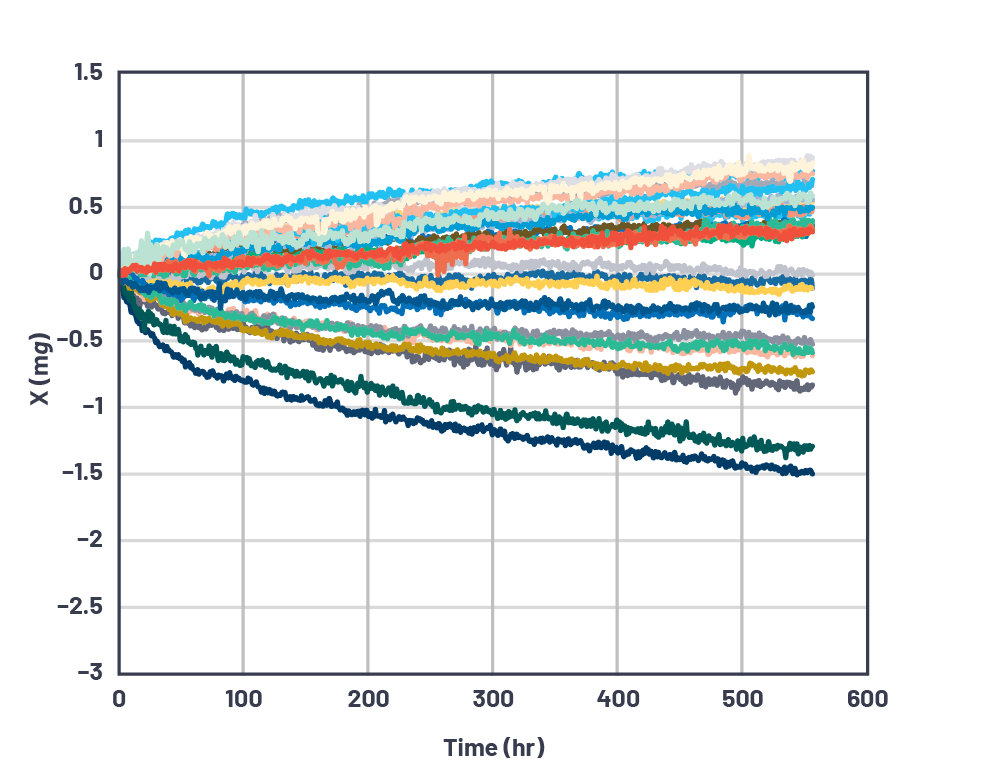
図10. ADXL355の長期安定性。23日間にわたり、オフセット・ドリフトを継続的に計測しました。
機械システムの設計における推奨事項
ここまでに説明した内容から、筐体と機械的な取り付け部分が、センサーに伝わる物理的な応力に影響を及ぼすことは明らかです。言い換えると、それらによって、加速度センサーによる計測結果が左右されるということです。一般に、筐体、機械的な取り付け、センサーは、2次(またはより高次の)の系を形成します。その応答には共振または過減衰が現れます。機械的な支持システムには、そうした2次の系(共振周波数とQ値によって定義される)に相当するモードが存在します。そうした要因について理解し、機械システムがセンサー・システムに及ぼす影響を最小限に抑える必要があります。そのためには、加速度センサーを使用するアプリケーションの帯域内において(過減衰による)機械的な減衰や(共振による)増幅を回避できるように、センサーを収容する筐体の形状、あらゆる接続部分、使用する材料を適切に選択しなければなりません。本稿では、設計時に考慮すべきすべての事柄を網羅し、詳細に解説することはできません。そこで、以下では、設計時に役立つ実用的な事柄をいくつかピックアップし、簡潔にまとめることにします。
プリント基板、筐体、機械的な取り付け部分
まず、プリント基板、筐体、機械的な取り付け部分に関する推奨事項を紹介します。
- プリント基板は剛体基板にしっかりと取り付けます。プリント基板の裏面では、接着剤と併せて取り付けネジを複数使用します。そうすれば、最良の支持を実現できます。
- 加速度センサーは取り付けネジまたは留め具の近くに配置します。プリント基板が大きい(数インチ)ものである場合には、その中央で複数の取り付けネジを使用します。それにより、プリント基板が低い周波数で振動するのを防止することができます。この種の振動は、加速度センサーによって計測されてしまう可能性があります。
- プリント基板の機械的な支持が溝や舌状構造だけによって行われている場合には、より厚いプリント基板(2mm 以上)を使用します。プリント基板の面積が大きくなる場合にも、系の剛性を維持するために、より厚さのあるものを選択します。特定の設計に最適なプリント基板の形状や厚さを求めるには、「ANSYS」などの有限要素解析ツールを使用するとよいでしょう。
- 構造ヘルス・モニタリングなどのアプリケーションでは、センサーによる計測を長期間にわたって実施します。そのため、センサーの長期安定性が重要な要素になります。パッケージ、プリント基板、接着剤の材料については、機械的特性の経時劣化/経時変化が最小限に抑えられるものを選択する必要があります。そうした変動が原因でセンサーにかかる応力が高まり、オフセットが生じてしまう可能性があるからです。
- 筐体の固有振動数は、根拠に乏しい推定値ではなく、なるべく確かな値として算出する必要があります。簡単な筐体の場合には、固有振動モードの計算を実施してください。より設計が複雑な筐体の場合には、有限要素解析ツールを利用するとよいでしょう。
- ADXL355 をボードにハンダ付けすると、応力が蓄積されます。これは、最大数 mg に達するオフセット変動の原因になることがわかっています。この影響を軽減するためには、プリント基板のランド・パターン、サーマル・パッド、銅パターンを介した伝導経路を対称に配置するとよいでしょう。ADXL355 のデータシートには、ハンダ付けに関する指針が記載されています。それに厳密に従ってください。また、場合によっては、キャリブレーションの前にハンダのアニール処理や温度サイクル処理を行うとよいでしょう。それらの処理により、蓄積した応力を解放できるからです。その種の処理は、長期安定性の問題を管理する上で有用であるということが確認されています。
ポッティング材
ポッティング材は、筐体内部の電子デバイスを保護することを目的として広く使用されています。しかし、加速度センサーのパッケージがオーバーモールド・プラスチックをベースとするLGAなどである場合、ポッティング材を使用するのはお勧めできません。なぜなら、ポッティング材と筐体の材料とでは温度係数が異なるからです。そのことが原因で、センサーに圧力が直接加わり、オフセットが発生してしまいます。一方、ADXL355のように、気密封止のセラミック・パッケージが使われている場合であれば、温度係数の影響を十分に回避することができます。ポッティング材の経時劣化は、プリント基板に応力が蓄積される原因になります。その結果、シリコン・ダイがわずかに反り、センサーに歪みが生じる可能性があります。一般に、高い経時安定性が求められるアプリケーションでは、加速度センサーにポッティング材を適用するのは避けた方がよいでしょう。なお、ポッティング材の代わりにパリレンCのような低応力のコンフォーマル・コーティングを適用すると、ある種の防湿層としての効果が得られます8。
エア・フロー、熱伝導、熱平衡
加速度センサーの性能を最大限に引き出すためには、本稿で指摘した事柄について慎重に検討を行った上でシステムを設計します。完成したシステムを、温度安定性の面で最適化された環境で利用できれば理想的です。本稿で示したように、わずかに温度が変化しただけで、加速度センサーのダイにおける熱応力の差が原因となって予期せぬ結果が生じることがあります。以下、熱に関連するいくつかのヒントを示しておきます。
- プリント基板において、加速度センサーはその温度勾配が最小になるように配置する必要があります。例えば、大量の熱を発する可能性のあるリニア・レギュレータの近くに配置するのは避けなければなりません。これに反すると、MEMS センサー全体に温度勾配が生じ、時間と共に変化するレギュレータの電流出力に応じて性能が変動する可能性があります。
- センサー・モジュールは、できればエア・フロー(空調システムなどを含む)から離れた場所に配備します。その目的は、頻繁に生じる温度変動を回避することです。エア・フローの近くに配備せざるを得ない場合には、パッケージの外部/内部で断熱する方法を用意すべきです。伝導と対流という 2 つの熱経路について考慮しなければならないことにも注意してください。
- 稼働環境における熱的変化を避けられないアプリケーションでは、環境の熱変動を抑えられるよう熱容量の大きい筐体を選択することが推奨されます。
まとめ
本稿では、高精度の加速度センサーであるADXL355を例にとり、環境からの影響や機械的な影響によってその性能がどのように変化するのかを明らかにしました。優れた判断力を持つ技術者であれば、システム・レベルの性能に主眼を置きつつ包括的な設計を行うことで、卓越した性能を発揮可能なセンサー・システムを構築できるはずです。私たちは、日々の暮らしにおいて多大な量のストレスを受けています。ただ、人々の命を脅かすのはストレスそのものではありません。加速度センサーの場合と同様に、ストレスに対してどのような反応を示すのかを把握することが重要です。それにより、ストレスに適切に対処することが可能になります。
著者について
この記事に関して
産業向けソリューション
製品カテゴリ
{{modalTitle}}
{{modalDescription}}
{{dropdownTitle}}
- {{defaultSelectedText}} {{#each projectNames}}
- {{name}} {{/each}} {{#if newProjectText}}
-
{{newProjectText}}
{{/if}}
{{newProjectTitle}}
{{projectNameErrorText}}